«Жизненный цикл» изделия от составляющих до готовой вещи, или как Cersanit автоматизировал производство с «Клеверенс»
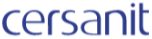
CERSANIT — это 12 современных заводов, оснащенных новейшим оборудованием, которые производят все для ванных комнат: от керамической плитки до акриловых ванн и мебели для санузлов. Продукция компании представлена в 44 странах по всему миру.
CERSANIT занимает шестое место в мире по производству керамической плитки и десятое место в мире по производству санитарной керамики.
https://cersanit.ru/
Но процесс массового изготовления товаров — это не только конвейеры и роботы. Это ещё и внутреннее перемещение заготовок между участками и полный «жизненный цикл» изделия от составляющих до готовой вещи. Компания Cersanit выбрала программную платформу «Клеверенс» для того, чтобы иметь возможность прослеживать путь изделия на всех этапах производства и повысить точность учёта. Для выполнения доработок в Mobile SMARTS обратились к специалистам компании «Кайтос».
Подробное описание
Как производится керамическое изделие? Грубо говоря, «лепят» из глины. Только давно не вручную, а при помощи техники: машин-роботов. Затем сушат, покрывают глазурью и «запекают» в печи. А далее уже идёт сортировка-упаковка готовой продукции. Всё это обычные складские процессы. Но как не запутаться, если через цех проходят сотни тысяч изделий в месяц?
Компания Cersanit известна во всём мире. Поставляет на рынок керамическую плитку, ванны, санфаянс премиум класса. Центральный офис находится в Москве, а заводы в нескольких городах России. В Сызрани, например, находится завод по производству санфаянса. Объёмы выпускаемой продукции огромные — более ста тысяч изделий в месяц. Весь учёт ведут сейчас в «1С: УПП». В планах сменить систему учёта на ERP.
В качестве дополнительного средства контроля на всех этапах производства использовали физические метки, которые ставили на изделия в местах крепления раковины или унитаза к стене — своеобразная физическая печать мастера участка. По этому отпечатку можно было отследить кто ответственный за изготовление данного конкретного изделия.
Задачи
Учёт на производстве важен не только для понимания объёмов выпускаемой продукции. А также для сбора статистики по браку и другим показателям. Вот только не всегда бумажные носители позволяют отразить полную картину брака или статистику списаний, так как имеют свойство теряться, либо сотрудники просто забывают заполнять необходимые акты.
Руководство компании Cersanit хотело повысить точность учёта брака, чтобы понимать, на каком из этапов производства он чаще всего образуется, и найти удобный инструмент проверки качества работы сотрудников и сбора статистики.
Прослеживаемость пути изделия на производстве и автоматизация производства — это основные задачи, которые ставил перед нами IT-директор «Церсанита». Лучшим программным решением, позволяющим реализовать пожелания заказчика, был «Клеверенс», так как эту платформу можно дорабатывать и переписывать — код открытый, софт гибкий.
А установленный на мобильный компьютер, он становится полноценным полностью автоматизированным рабочим местом. Мы продемонстрировали заказчику макет, рассказали, какие доработки нужно будет выполнить, сколько времени на это потребуется. И, после согласования, приступили к работе.
Как произвести 100 тысяч изделий в месяц, не потеряв ни одной единицы? Как учитывать различные виды производственного брака? Как отслеживать одновременно работу 100 человек в смене? Ответы на эти вопросы нашли специалисты компании «Кайтос» совместно с сотрудниками Cersanit.
Есть несколько производственных этапов. Каждый производственный этап — отдельная операция на терминале сбора данных. Этапы друг от друга отличаются, но имеют схожую структуру.
На первом этапе машина отливает, например, раковины — в специальной форме на несколько изделий. На ТСД эта операция выглядит следующим образом: открывают документ, сканируют литьевую форму с изделиями, и на моменте выполнения операции присваивают штрихкод к каждой отдельной раковине. Затем берут подготовленные этикетки, их ещё называют деколь, сканируют на каждом этапе производства и вешают на изделие.
Далее идёт процесс агрегации — когда изделия вынимают из формы и объединяют в партию. Для передачи на следующий производственный участок при помощи транспортной единицы, выступающей в роли складской ячейки. Делается это для того, чтобы не сканировать терминалом каждую снятую с конвейера раковину отдельно, а учитывать сразу по ячейкам — на 40 штук, например.
На следующий этап производства изделия принимают в разрезе транспортной единицы. Если количество раковин по документу на ТСД не сходится с количеством после сканирования, то можно провести инвентаризацию. Чтобы понять, какого штрихкода и, соответственно, изделия не хватает. Недостающие позиции выбраковывают и списывают по определённому коду брака. Такую выбраковку можно делать на каждом производственном участке.
Кодов брака много. Мы выделили 3 основных:
- производственные — что-то не то сделали,
- человеческий фактор — разбил,
- и потери — пропало, переложили и сразу не нашли.
При этом мастер может забраковать изделие при проведении инвентаризации.
Штрихкоды раковинам, унитазам и другим изделиям присваивают перед отправкой на второй производственный участок: после того, как они прошли первичную проверку и признаны годными. Такой порядок обусловлен тем, что этикетки (деколь) дорогие, и нет смысла впустую тратить их на изделия, которые возможно будут забракованы сразу после формовки. После обжига в печи этикетка впаивается в керамику и остаётся навсегда.
Третий этап производства тоже принимает изделия в разрезе транспортной единицы. Здесь происходит передача полуготовой продукции с одного участка на другой по документам. Транспортную единицу отправляют на первый производственный этап как свободную. А раковины или унитазы передают на следующий участок.
С «Клеверенсом» и ТСД несколько человек могут спокойно работать с одной транспортной единицей одновременно. И наоборот: один человек может работать с несколькими ячейками сразу.
Для того, чтобы избежать путаницы в штрихкодах изделий и ячеек, мы сделали их принципиально разными. Так же и коды брака не имеют ничего общего с остальными ШК. Штрихкоды изделий — это аналог маркировки, только внутренний.
На уровне терминала сотрудник Cersanit работает с одним документом, в котором есть подуровни. А вот в системе учёта подуровни выступают как разные документы — как если бы в стандартной операции «агрегация» переключались между коробками. Но переключение более оперативное. Соответственно, система Mobile SMARTS однозначно может понять, что работа ведётся в рамках одной и той же транспортной единицы.
Следующие три участка предназначены для дальнейшей обработки изделий. Если на всех предыдущих этапах продукция списывается по браку безвозвратно, то здесь санфаянс не считается окончательно забракованным. То есть любое изделие могут вернуть на доработку или исправление/починку. Если на каком-то из этих участков обнаружили трещину, можно передать условный унитаз на специальный участок, где его «починят» в зависимости от рода повреждения. Все перемещения выполняются посредством считывания ШК и передачи по документам.
Для этих участков есть собственные коды брака, которые означают, что изделие нужно продиагностировать и «отремонтировать». В этом случае продукцию отправляют на соответствующий дефекту этап участка, там её мастер проверяет и выносит вердикт: если можно «реанимировать», отправляет на исправление. Если же ремонт невозможен, то изделию присваивается финальный код брака, и оно окончательно списывается. Либо мастер считывает соответствующий ШК, который маркирует в системе изделие как годное.
На всю смену у каждого сотрудника Cersanit есть только 1 рабочий документ. Мы сделали так, чтобы они не путались, переключаясь между документами. Потому что в «Клеверенс» создание документа — достаточно длительная операция: зайти в операцию, нажать «создать», далее зайти в меню, там нажать «сканировать». Теперь сотрудник в начале смены создаёт для себя один рабочий документ и всю смену с ним работает — во избежание долгих манипуляций.
При этом выгрузка в 1С происходит сразу после каждого сканирования. Это всё нестандартно по отношению к «Клеверенсу», потому что в любом продукте выгрузка в систему учёта идёт после завершения документа. А на производстве разница передачи продукции между некоторыми участками — всего несколько минут. И пока изделие за эти несколько минут везут на другой участок или этап, информация о том, что там с ним дальше делать, должна отразиться уже у сотрудников другого участка. Каждое сканирование ШК/этикетки/деколи завершается автоматически.
Передача изделий с участка на участок при помощи ТСД позволяет контролировать очерёдность этапов: если она не соблюдена — отсканировал ШК на третьем участке раньше, чем на втором, — система сообщит, что этого делать нельзя, так как нарушена последовательность.
Такую систему ввели ещё и для того, чтобы замерить производительность на каждом конкретном участке. То есть если какой-то этап пропустят — один раз, два, пять — актуальные данные практически невозможно будет получить. Поэтому пропуск производственного этапа ограничили тем, что ТСД «ругается». И последовательность прохождения изделием всех участков строго соблюдают.
Единственный этап, на котором изделия не проходят через ТСД — этап сортировки. Здесь готовые изделия сортируют по паллетам. На этом участке мастера сканируют всю продукцию при помощи обычного сканера штрихкодов, а информация сразу отображается в системе учёта на компьютере.
Сортировку разделили на 2 этапа:
- отгрузка на упаковку паллетами — это третья транспортная единица. По принципу работы совпадает с другими этапами, где учитываются складские ячейки.
- упаковка/приёмка в разрезе паллет.
Эти 2 этапа специалисты компании «Кайтос» разработали, но в эксплуатацию ввели не сразу.
Интересно то, что иногда, чтобы исправить какой-то дефект, санфаянс обжигают дважды. Но ни в коем случае нельзя его ставить в печь третий раз. Изделие просто взорвётся. И вот терминалы позволяют контролировать эту процедуру: система будет «кричать»: «Нельзя этого делать!».
Раньше отслеживали все производственные этапы по физическим печатям. Тоже контролировали, кто сделал брак и когда. Сейчас же каждый сотрудник работает под своей «учёткой». Все данные синхронизируются с 1С. И теперь можно отсканировать ШК и увидеть кто, когда и сколько раз притрагивался к изделию.
Финальный этап — упаковка: когда в коробку, вместе с пенопластом, упаковывают полностью готовое изделие. Далее только передача на склад хранения готовой продукции через WMS. На этом заканчиваются производственные процессы, но не заканчивается автоматизация.
Специалисты компании «Кайтос» разработали несколько дополнительных функций, облегчающих работу и учёт на производстве:
- Перемещение между этапами.
Если какое-то изделие фактически дошло до сортировки, но в системе отмечен только этап заливки в форму, мастер участка может открыть на ТСД «Мастер интерфейс» и переместить «заблудившееся» изделие принудительно на нужный участок. - Контроль брака.
Это так называемая принудительная возможность вернуть изделие из брака. Например, раковину не досчитались на первой транспортной единице и списали. А на следующей транспортной единице эта раковина была лишней среди унитазов. В этом случае мастер участка сканирует штрихкод изделия и возвращает его в систему. - Замена ШК.
В случае потери штрихкода изделия можно создать новый.
Мастер интерфейс подкинул нам головной боли в плане разработки. Потому что нужно, во-первых, правильно списать изделие с предыдущего участка. А во-вторых, правильно оприходовать на нужный участок, с указанием всех дополнительных разрезов. И обязательно учесть, что коды брака/списание, принципиально отличаются.
Весь проект по внедрению специалисты компании «Кайтос» выполняли удалённо на базе программной платформы «Клеверенс». Со стороны Cersanit в проекте принимали участие системные администраторы, сотрудники производства, директор по производству, начальники участков, мастера участков. Приезжал директор всех производств России — чтобы ознакомиться с тем, как работает система. Установку на предприятии делали системные администраторы Cersanit своими силами, а начальники этапов масштабировали на сотрудников и участки. Проект разработали специально для завода по производству санфаянса в городе Сызрань.
Обмен между учётной системой и терминалами настроили по Wi-Fi. Сейчас дополнительно решаем этот вопрос, так как иногда сеть просто «пропадает» и обмен выполняется некорректно: не после каждого сканирования, а когда появится сеть. С «1С-кой» много технических вопросов решали, потому что если «лагает» система учёта, то автоматически подвисает и ТСД.
В «Клеверенсе» тоже было несколько ошибок. Например, чёрные полосы вместо названия изделия. Возникало это рандомно в рамках одного документа. Это был баг с отображением фона. Исправили заливку фона — заменили на прозрачный для всех позиций в документе.
Ещё со штрихкодами литьевой формы помучились: первично ШК присваивается форме, когда её только устанавливают. Затем сканируют этот штрихкод, и он присваивается изделиям. При считывании ТСД строка должна автоматически «перепрыгивать» на следующую. А у нас она никак не хотела этого делать — застревала на одном и том же изделии. Решили тем, что «Клеверенс» выпустил новый apk.
С терминалами MobileBase DS5 тоже не сразу всё гладко было: ТСД с клавиатурой. Есть поле для ручного ввода штрихкодов. Но когда после ввода нажимали кнопку Enter, система никак не реагировала. «Клеверенс» помог — выпустил новый релиз.
В планах руководства Cersanit ещё ввести дополнительные операции, которые можно будет выполнять при помощи терминалов, и внедрить на складе готовой продукции «Склад 15» для проведения инвентаризаций. Дополнительно на производстве уже реализовали возможность проводить ревизии с ТСД, так как на каждом участке хранятся какие-то остатки продукции.
Из-за того, что на производстве достаточно агрессивная среда, терминалы сбора данных периодически заменяют новыми. Для тестирования всех разработанных операций один терминал передали специалистам компании «Кайтос».
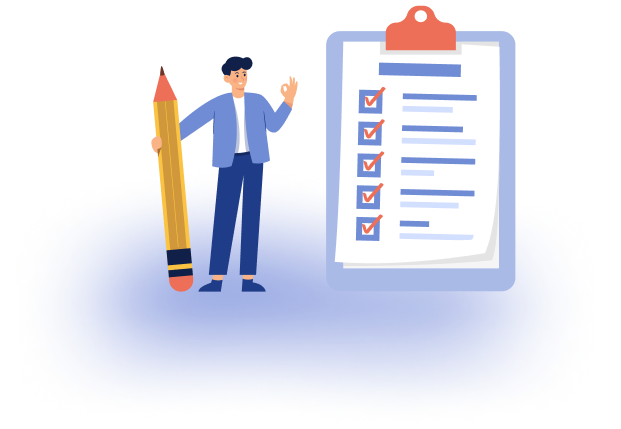
Пройдите короткий опрос и за 3 шага узнайте стоимость автоматизации в вашей компании!
Результаты опроса помогут рассчитать стоимость готового решения точнее
Рассчитать условияРезультаты
Производственные процессы всегда представляют собой достаточно сложную цепочку. Так как помимо изготовления какой-либо продукции нужно правильно выстроить систему учёта, наладить последовательность этапов, постоянно проводить аналитику.
Компания Cersanit получила дополнительный инструмент контроля брака и возможность собирать актуальные аналитические данные с участков, а также смогла повысить качество производства в целом. Теперь начальники участков могут отслеживать KPI сотрудников, ранее таких данных не было.
До введения в работу терминалов сбора данных на производстве Cersanit было только 4 этапа. Сейчас количество этапов выросло вдвое. Но совсем не сложно проследить весь жизненный путь изделия от куска глины до конечного потребителя, благодаря тому, что программная платформа «Клеверенс» и мобильные компьютеры позволили достичь высокой точности учёта на каждом из этапов в отдельности.
повысили точность учёта брака
автоматизировали производство
достигли высокой точности учёта на каждом этапе
Партнер
Компания «Кайтос» занимается комплексной автоматизацией предприятий на базе программных продуктов 1С:Предприятие. Основное направление деятельности компании — проектное внедрение и системная интеграция 1С.
Специалисты «Кайтос» оказывают услуги по разработке нового функционала 1С, оптимизации скорости работы системы, интеграции 1С с внешними системами (обмен данными), подключению и настройке торгового оборудования, адаптации и внедрению программного обеспечения Mobile SMARTS.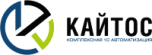
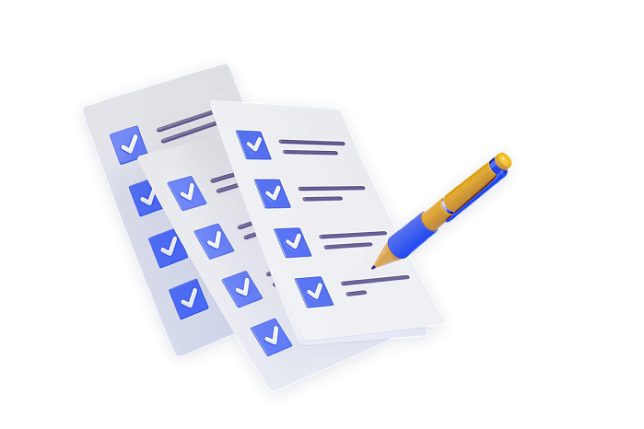
Если у вас остались вопросы, вы можете скачать PDF-руководство по автоматизации магазина или задать его специалисту
Скачайте PDF-руководство и узнайте ввсю необходимую информацию по автоматизации магазина
Скачать руководствоПримененное оборудование и программное обеспечение
У вас остались вопросы?
Наши эксперты готовы ответить на любые вопросы — спрашивайте